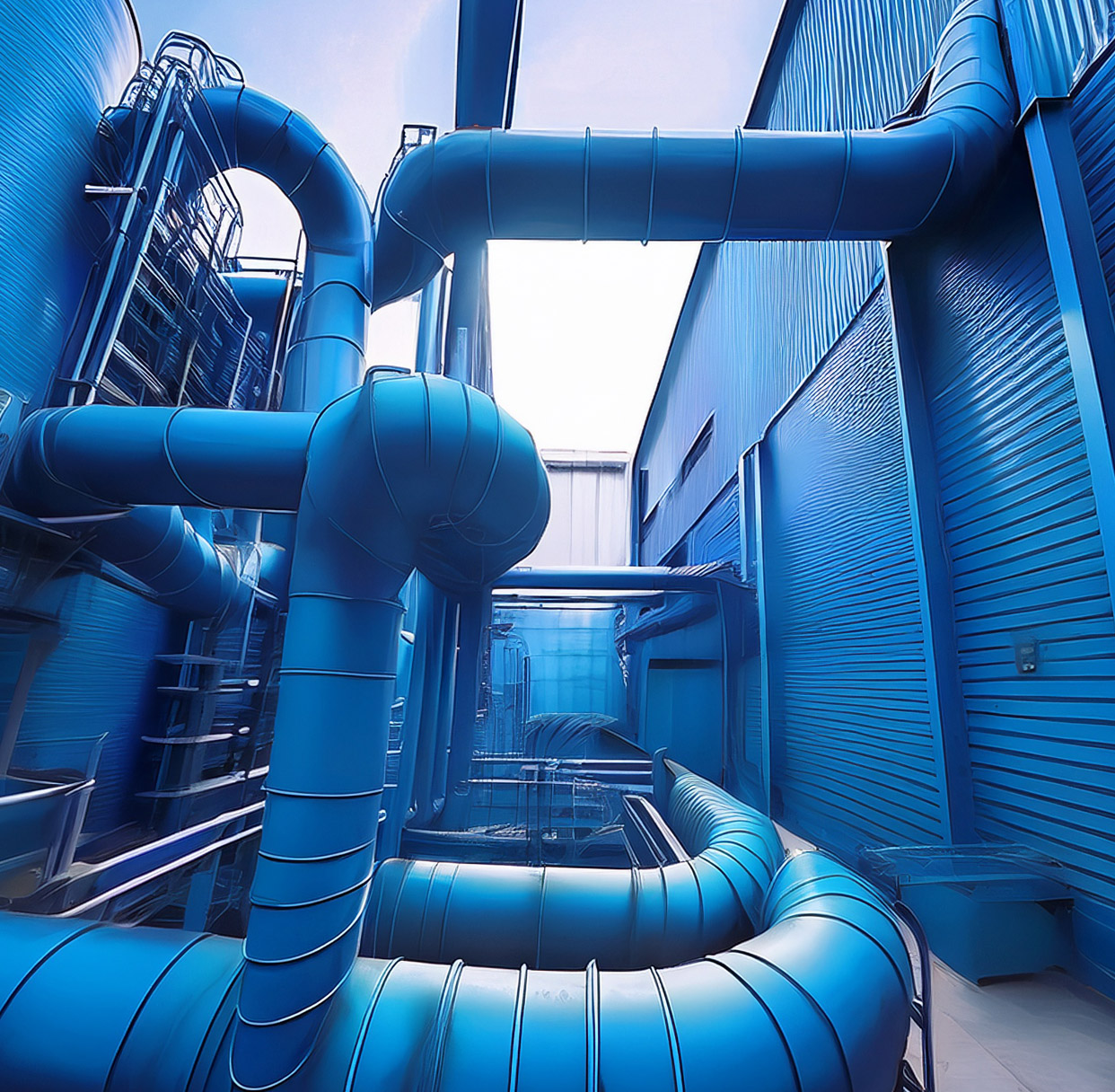
FAQ
FAQ
1. What is Local Exhaust Ventilation (LEV)
LEV or Local Exhaust Ventilation is a type of ventilation use to control exposure to potentially hazardous substances. Exhaust or extraction ventilation systems are normally classified in two different generic groups: a) General exhaust systems and b) the Local exhaust systems.
General exhaust ventilation can be used to control heat and/or remove contaminants generated in a space by dilution with large quantities of fresh air.
Local exhaust ventilation systems operate by capturing a contaminant at or near its source and moving it away to a place where nobody is working or to an air cleaning device.
2. What makes up an LEV system?
LEV systems are made up of four basic elements: the hood (that captures the contaminate), the duct system that helps move the contaminant away from the workplace, the air cleaning device that removes the hazardous substance and the fan which provides energy to move the contaminated air through the systems.
3. Is it a legal requirement to test an LEV system?
Yes. The legal requirement to examine and test LEV systems are contained within the CoSHH Regulations.
They control the way in which all substances hazardous to health (i.e. raw materials, products, by-products, wastes etc) are used, stored, handled on premises.
Substances Hazardous to Health are defined in a 5 part definition:
a) Listed in CHIP Regs as toxic, very toxic, harmful, corrosive or irritant.
b) WEL specified (see HSE Guidance Note EH40)
c) Micro-organism which creates a hazard to health of any person
d) Dust of any kind, when present at a substantial concentration in air
e) Anything else not mentioned above which poses a hazard to health
4) What do the COSHH regulations require an employer to do?
Reg 6 i) Assess the risk - this means looking at the substances used or produced, where and how they are produced, the quantities, concentrations and other such variables.
Who uses them or is exposed to them and how they are used.
What controls are in place to prevent harm?
From all of this to summarise the actual potential risks to the employees (or visitors, contractors etc) from these substances and whether the controls are adequate to prevent harm.
Reg 7 ii) Prevent Exposure - Provide Controls - this means engineering controls - not merely to provide personal protective equipment (eg respirators) - to a level of control which goes "so far as is reasonably practicable".
Reg 8 iii) Use Controls - duty on employer to ensure that controls are properly and fully used!
Duty on employee to make full and proper use of controls, personal protective or other equipment and to report defects "forthwith" to employer.
Reg 9 iv) Maintain, Examine& Test Controls - must ensure that CONTROLS
(Note - not just LEV but all controls) are maintained in:
EFFICIENT STATE
EFFICIENT WORKING ORDER
GOOD REPAIR
For Local Exhaust Ventilating (LEV) Plant these must be:
"thoroughly examined and tested at least once in every 14 month period ...." or at intervals specified in Schedule 3 or CoSHH Regs.
For other controls the thorough examinations and tests shall be at "suitable intervals".
Reg 10 v) Monitoring Exposure - this is required where it is necessary to prove and to show that employees are not being exposed to unacceptable levels of exposure i.e. to prove that the control systems are working efficiently.
Vinyl Chloride monomer and electrolytic chrome plating emissions are specified as to frequency.
Reg 11 vi) Health Surveillance - required where it is "appropriate" for exposed employees to be under surveillance.
Deemed "appropriate" for substances specified in Schedule 5 to the Regulations and for any other substance where there is a known disease or adverse health effect which could occur in the work circumstances.
Reg 12 v) Information, Instruction & Training - every employee must be given this sufficient for him to know:
- the risks to health from his exposures at work
- the precautions which should be taken
Employer is under a duty to ensure that anyone carrying out duties under the Regulations has had the necessary information, instruction & training.
4. How often do systems need to be tested?
Regulation 9 of COSHH states that control systems should be "thoroughly examined and tested at least once in every 14 month period ...." or at intervals specified in Schedule 3 or CoSHH Regs. For other controls the thorough examinations and tests shall be at "suitable intervals". Most customers test their system once a year.
5. How much does it cost to have systems tested.
The cost of the examination and testing will depend on several factors, including, the number of systems on a site to be tested, the size and complexity of the system(s); site access restrictions. The way we work out the cost of the testing is simple, it's our estimate of how long we will be on site plus how much time it will take to write the reports times our day rate. Because we have been carrying out LEV testing for a long time we are very good at determining how long it will take. This means we can give you a fixed competitive cost.
ESP will be pleased to provide a firm and fixed quotation for your LEV examination and testing. To obtain a free quotation for the examination and testing of your local exhaust ventilation system(s), please fill out the form in the contact section.